Milstein hexagonal and triangular modules fit together to build simple, practical furniture from your ecobricks. All you need is a dozen to get going!
Milstein modules can be made by anyone, anywhere using simple materials and methods. Using either silicone or tube-banding methods, ecobricks can be put to use right away in applications that embody circular and regenerative principles.
Milstein Modules can be used on their own as seating or combined like LEGO to create horizontal surfaces. People use them for tables, beds, benches and even stages! Milsteins are often combined with Dieleman Modules to create Ecobrick Open Spaces.
Milstein Modules
Its easy to make versatile, durable and super practical indoor furniture that can be used in all sorts of ways.

A rainbow milstein module | England, UK

Some of the first modules ever made | Tadjian, Philipinnes
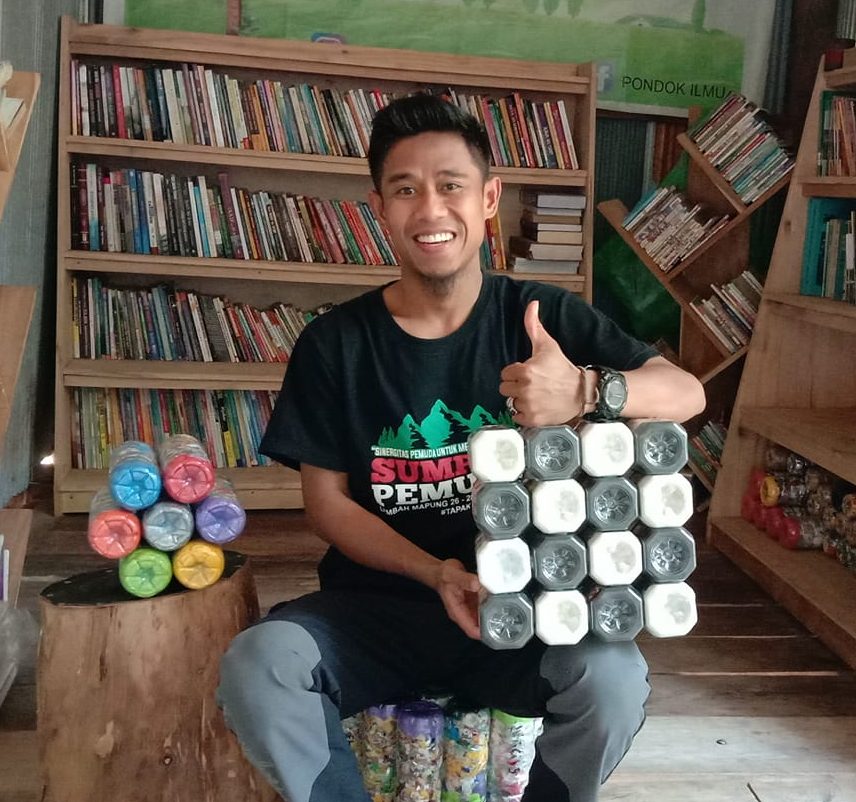
A module made from square bottles | Indonesia

Simple and practical | Jogja, Indonesia.

A circular cob and ecobrick construction.
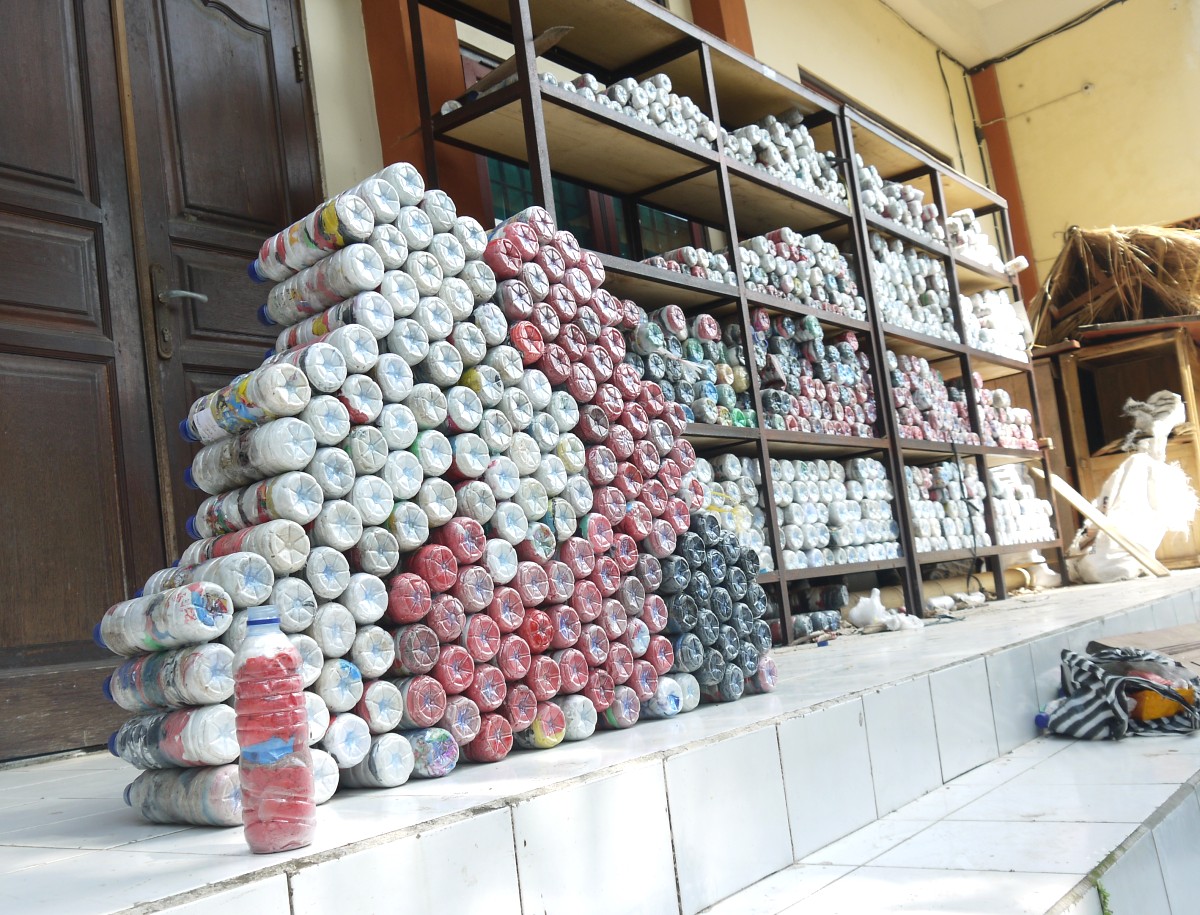
Modules can be easily stored too | Bali, Indonesia.
Milstein modules require a minimal amount of ecobricks to start. All you need is a dozen or so ecobricks of the exact same size to get started. You can use silicone or old inner-tubes to combine them. Modules are a short-term circular application that with proper care will last years before needing repair.
The GEA approved methods here do not damage the ecobricks during their life cycle. This means that modules can easily be repaired or they can be disassembled and the ecobricks put to use in a new application.
Milstein Modules can be used individually as convenient seats that are sliding and stackable. Hexagon milstein modules can be like honeycomb to create horizontal surfaces like tables, beds, benches and more. Triangle modules can be interlocked with hexagons to make a second level. For full vertical building see Dieleman module.
Ecobrick modular applications are indefinitely scalable. The more you have the more you can build. Eventually with hundreds of milstein and dielman communities create Ecobrick Open Spaces— interactive community spaces that can be built, un-built, and built again during conferences and gatherings to serve the needs of the moment.
It is important to use modules indoors. Ecobricks should never be exposed to the sun. Ultra violet (UV) rays will gradually fade the ecobricks colors and photo-degrade the plastic bottle’s PET. After only two or three years, the brittle bottle risks crack and burst, releasing all our hard packed plastic. Keeping modules entirely indoors and out of the sun is essential to preventing degradation.
Variations
There are several ways to make milstein modules to maximize versatility.
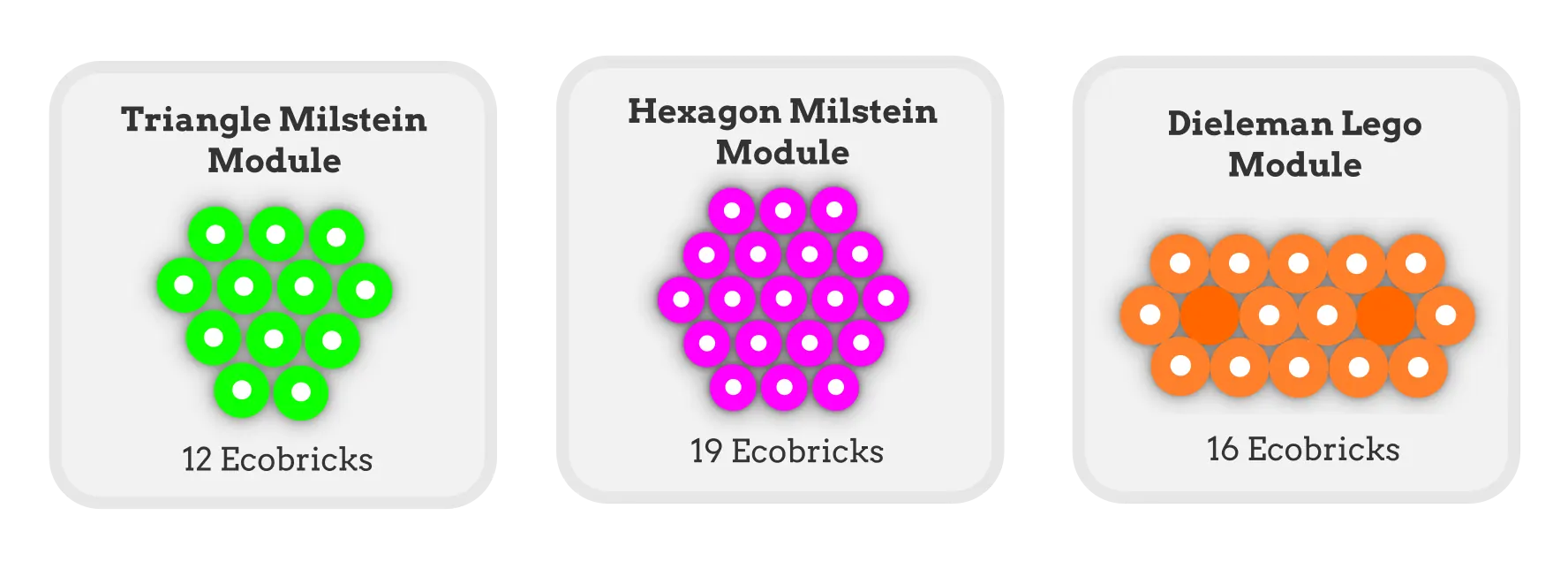
Hexagon milstein modules are made with 19 Ecobricks, these modules make the best stools and are the most versatile. Hexagon modules can combine them like honey-comb. Use them to build tables, stages, walls and more.
Milstein modules can also be used as LEGO. Hexagon and triangle modules can be stacked on-top of each other in a way that interlocks. This is a nifty and practical way to build a second level to make chairs and tables.
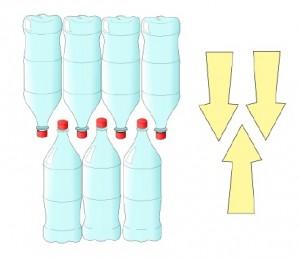
Dieleman modules are another type of ecobrick module. They are made with 16 ecobricks and enable vertical and horizontal building. We have a special on Dieleman Modules.
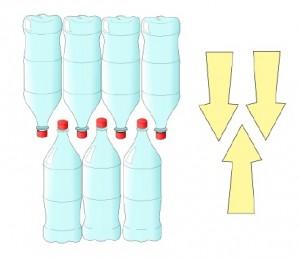
Silicone Method
The original and most enduring making milstein modules is using silicone sealant.
Learn from the GEA Master Trainers in Indonesia how to make ecobrick module
Normal, everyday silicone sealant can be used to make mistein modules.
This is the original way to make modules, by using silicone sealant. Builders' silicone, also known as “caulking” and “aquarium sealant” is inexpensively found in hardware stores around the world. Silicone is non-petroleum. It is not a type of plastic, and it does not degrade into microplastics, nor leach toxins or interfere with ecological cycles. Silicone breaks down into silicon and oxygen when it degrades.

This is almost a zero-waste process! The HDPE silicone tube can be easily recycled and/or used in your projects. See the chart at the bottom of the page on how this method compares with the tire banding method.

Preparation
To start you will need a well ventilated space, a perfectly flat surface, a caulking gun, a tube of silicone, a knife and of course, your ecobricks. Hopefully, you’ve followed GEA ecobrick making and storage directions, so that you can easily pick a selection of colored ecobricks to make a cool pattern.
There are many different types of silicone – our experience is that the cheapest all-purpose product (not special-brand or special purpose version) at your local hardware store works best. Avoid colored silicones and stick to clear.
Safety
Make sure you’re working outside or with a fan, because as silicone cures it releases vinegar gas (acetic acid). It’s not good for you or your helpers if you breathe too much of this. Ideally, have a partner assist: one person holds and places the ecobricks, the other operates the silicone gun.
To Start…
- Go through your available ecobricks and create a beautiful pattern using the bottom colors of the ecobricks. Arrange your ecobricks in the desired module pattern with the bottom down.
- When your pattern is set, remove the cap of the center ecobrick (this will help guide you as the module grows).
- Insert the silicone tube into your caulking gun and use your knife to cut the top off your silicone tube and the nozzle. Be sure to ecobrick the plastic cuttings!
Siliconing
- One partner removes the center ecobrick from the test arrangement and holds it for the other to silicone.
- Lay a single thick bead of silicone down the side of the ecobrick. The bead should be high, not squished or flat – this will help create the strongest bonds between bottles.
- Place the bottle down in the center of the flat space you’ve chosen. Take the next ecobrick, and press it gently against your center bottle. And you're off!
- Grab the third bottle. This time add two beads of silicone down the sides of the bottle (where the bottles will touch the two others). Gently press this bottle against the first two.
- Ideally your high silicone beads compress nicely, maximizing the contact surface.
- Continue adding ecobricks in this way, from the center outwards.
- Be sure as you press new bottles into the pattern that you do not disturb the bonds of the earlier bottles. Try to avoid repressing bottles together after they’ve been set. Undisturbed silicone joints are strongest.
- Be careful as you work to not lean over the pattern— the vinegar fumes from the silicone are strongest here. Always work from around the outside.
Finishing up
- Once all your bottles are all laid, its time to… wait!
- Do not move or even touch your module for the next two hours. After two hours, you can safely put the cap back on the center bottle and if necessary gently slide the modules (but it's best not to!).
- After 24 hours you can move the module.
- After 36 hours (i.e. when you can no longer smell the silicone drying) your module is good to sit and even stand on!
Banding Method
Tire banding is a simple technique for joining ecobricks together using 100% re-used materials.

A rainbox milstein module made with strong elastics | UK

A module being made by cutting up a motorcycle tire inner tube | Indonesia
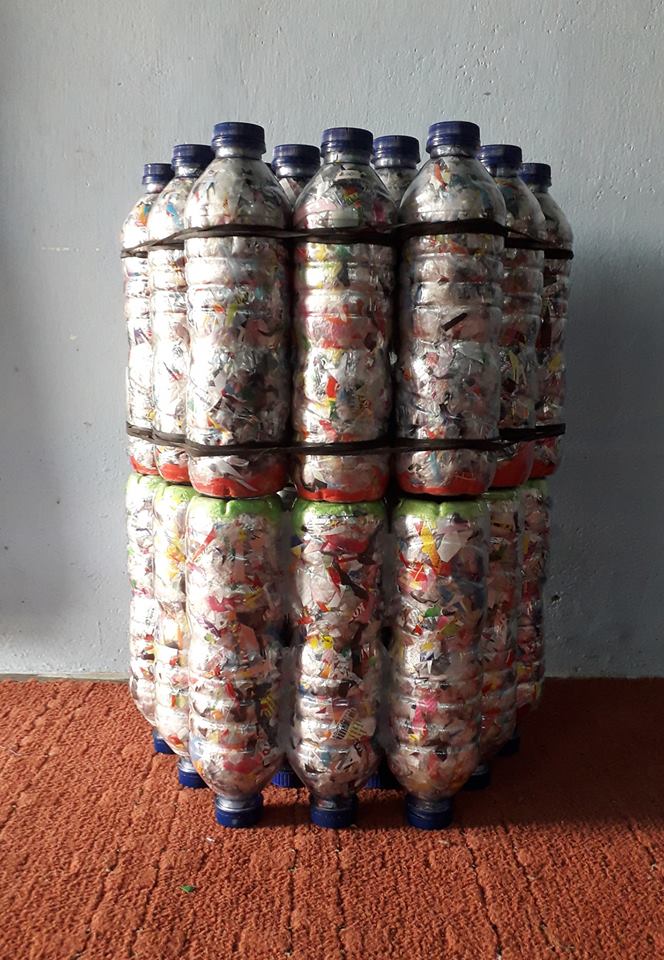
A comparison between tire banded and siliconed ecobrick modules. | Jakarta
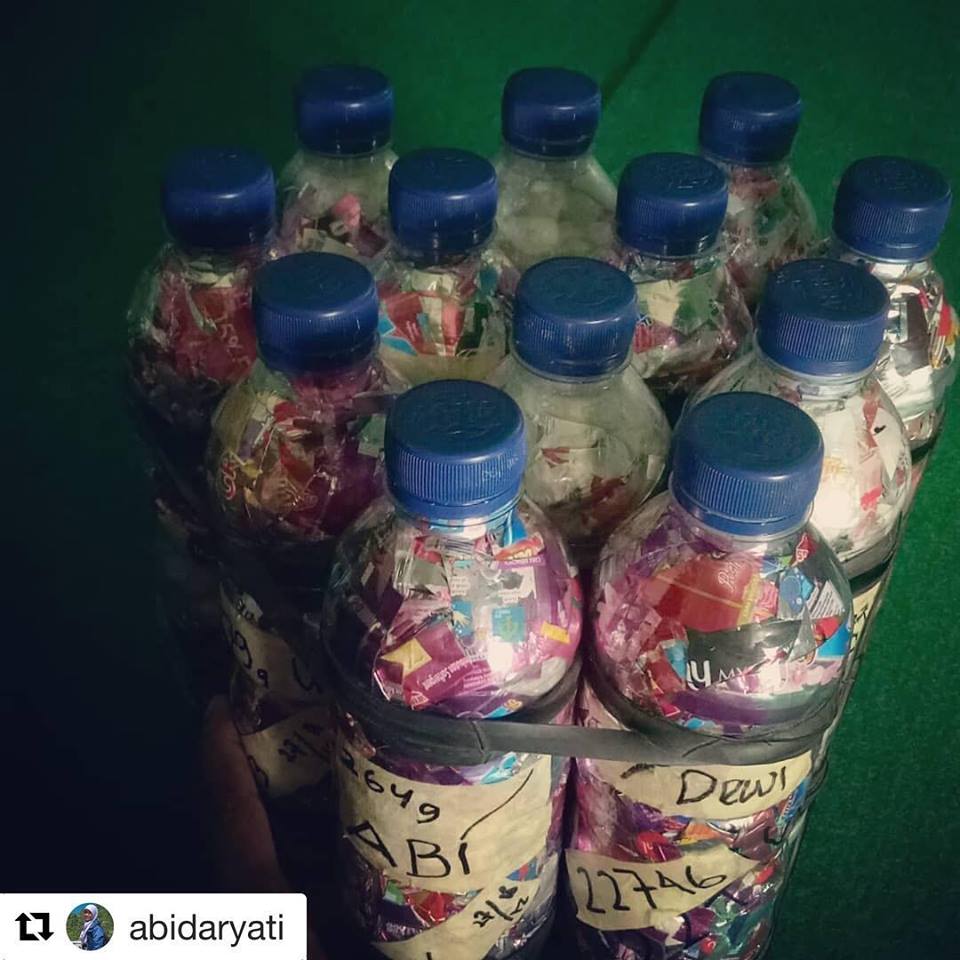
Thin tire bands make a triangle milstein module | Philippines

A tire banded module used to hold up a potted plant | Indonesia

A module being made by cutting up a motorcycle tire inner tube | Indonesia
With luck, you have a mechanics shop near you that works with motor bikes. By using the old inner tubes from motor cycles we can also connect our ecobricks together. Unfortunately, bicycle and car tires are too small and too big for the straightforward application of this method. But you’re welcome to try – it all depends on the diameter of your ecobricks and that of the inner-tube.
Unlike old methods of tying a stack of ecobricks together with a long vertical strip of innertube, in the tire banding technique, we cut the tubes horizontally to make many small elastic bands. Just like the siliconing method, we’re not permanently bonding the ecobricks together, so that later the module can be fixed or destroyed without damaging the ecobricks.
Like all ecobrick applications, the making process works best collaboratively. You’ll need a partner, some ecobricks and a wooded stick. Your ecobrick packing stick or an earthwand will do the trick!
Getting Started
We’ve found that motor cycle tires are ideal for binding 600ml bottles. Use only identical bottled ecobricks for one module. Really old inner tubes, or those that have been exposed to the sun won’t work – they will snap too easily.
- Take your scissors and cut across the inner tube to make a ring. As you cut the tube into bands, angle your cuts slightly so that the bottom of the band is slightly smaller than the top – about 1 centimenter on the bottom and 1.3 cm on the top. This will help you maximize the number of bands you can get out of the tube, while minimizing waste.
- Cut only about six bands to start as you will need to test the dimensions/elastacity of your bands before you cut the rest of the tire.
- Hopefully you’ve follow the recommended ecobrick making and storage methods so that you’re ecobricks have colored bottoms and are easily accessible. Arrange your ecobricks to make a pattern of colored bottoms (this will be the top of your module).
- Slide a band over the bottom and the top of your center ecobrick. Bring out the adjacent ecobrick. Slide the top and bottom elastics over the second ecobrick so that it is partnered with the first.
- Now connect your second ecobrick, in the same way to a third. In this way you’ll have three partners attached in a line.
- Push all three bottles together and connect bottle the first bottle, to the third. The ecobricks should be tightly bonded in a triad! They should not be able to slide back and forth or wiggle. If your bonds are too loose (or too tight!), go back to cutting your elastics. By adjust the thickness of your elastic you can adjust the tightness of your tube bonds.
- Once you’ve got a good feel for the sizing of your bands, cut the entire up into bands. You’ll eventually be able to put them all to use. See if you can do it without creating any waste snippets! Of course… every bit of excess cutting, you can put into an ecobrick (like the nozzle)! This makes this a zero-waste making method.
- Alright… that was the easy part! Now, connect ecobrick No. 4 to ecobrick No.3. Connect No. 4 to No.2…. Continue to add on ecobricks in this way. It won’t be easy, as the bonds will start to get tight and overlap. This is where working with a partner comes in handy.
- Have one partner hold the connected ecobricks and another adding the new ecobrick. Use a stick or earthwand to press down the elastics as you go.
- Continue adding ecobricks until you’ve completed your triangle or hexagon module.
- Use your stick to level out the elastics on the side so that they make a neat, level line around the outside.
- And, that’s it! Your module is good to go!
If you have used bottles of identical brand, the hexagon module top will fit perfectly into a triangular module bottom. Make more modules! Experiment with module size and back-to-back modules. Make cool stuff!
ℹ️ Learn more about our Mandalic Collaboration
Maintenance and Next Life
As in all ecobrick applications, be sure to keep your modules out of the direct sunlight. The sun will fade colors and degrade silicone, rubber and plastic.

An old module can be cut apart and its ecobricks reused.
All in all, you can expect an indoor module to last 3-5 years. After this time, the silicone bonds will begin to fail. Silicone modules, can be easily repaired by removing loose bottles, clearing off their old silicone, cleaning their surface and re-siliconing. The same goes for tire-band modules; simply reattach the bottle.
Next Life
When your module comes to the end of its life, use a sharp knife to cut the bottles out of the pattern. Be sure not to cut the PET of the bottle as you do so– often pulling the bottles apart will suffice.
For silicone modules, you can also use vinegar or isopropyl alcohol to weaken and dissolve the bonds. Clear the old silicone from the old bottles.& Your ecobricks can now be reused to make modules or applied in earth and ecobrick constructions.
You can safely dispose of silicone sealant in your garden, ideally in a sunny place. Silicone is not plastic, nor is it petroleum based. It degrades harmless back into its inorganic components of amorphous silica, carbon dioxide, and water vapor (SO, CO2, H2O).
Maintenance and Precautions
As in all ecobrick applications, be sure to keep your modules out of the direct sunlight. The sun will fade colors and degrade silicone, rubber and plastic.
With the tire banded modules it is critical to keep them out of the sun. Inner tubes are made from butyl rubber from petrochemicals. Inner tubes are highly susceptible to photodegradation and will weaken within weeks of UV exposure. Butyl rubber degrades by breaking down into small and smaller pieces similar to micro-plastics. These do not biodegrade and instead accumulate in the environment. Butyl rubber is seldom recycled, so it is best to pack broken pieces and cuttings into an ecobrick.
What's Next?
Milstein module applications are scalable in home and in community spaces. Keeping adding to your collection to build more with them.

An old module can be cut apart and its ecobricks reused.
The great thing about ecobrick modules is that their application is indefinitely scalable. In other words, the more modules you and your community make, the more things you can build with them. In Indonesia, some communities pool their modules together into a common collection that they then rent out to be used in eco-events.
These large scale applications of many modules are known as ecobrick open spaces— interactive community spaces that can be built, un-built, and built again during conferences and gatherings to serve the needs of the moment.
As you keep making modules consider also dieleman modules. This type of ecobrick module can be used to build with vertically as well as horizontally-- though, unlike Milstein modules, many are required in order for them to be practical
When your modules comes to the end of its life-- no worries! You can cut the ecobricks out from their silicone or rubber connections, then put them to next use. Earth and Ecobrick building is a great long-term application for used ecobricks.

Of course, you can also use your ecobricks to make another module too!

History
Milstein Modules were conceived and developed by Russell Maier, one the founders of the GEA, during his time in the Northern Philippines.
The history of the ecobrick module begins in the Northern Philippines in 2010. Requiring furniture for his home, but having no means to procure it, Russell Maier, did the next best thing – he made it with what was freely available. Living in a small village in the remote Northern Philippines, there weren’t any furniture stores near Russell’s home, but there were lots of ‘waste’ glass bottles! Under many houses in the village were stores of unrecyclable gin bottles that had accumulated over the years. Russell began to experiment with the square, brick-like glass bottles that his neighbours were only too happy to get rid of.
Through trial and error, with the help of Bianca Silva and Russell, discovered that silicone was ideal for attaching glass bottles together to make small modules. Together they created tables, chairs, lamps and much more. Russell exhibited his modular glass bottle furniture for the first time in the BenCab gallery in April 2012 with the help of Alvin Berto.
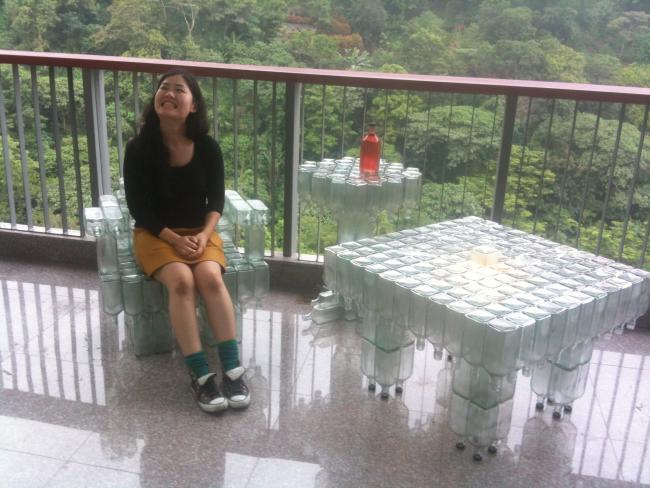
2014 BenCab Art Gallery, Baguio, Philippines.
As the ecobrick movement took off, an abundance of ecobricks were being produced throughout the Northern Philippines.
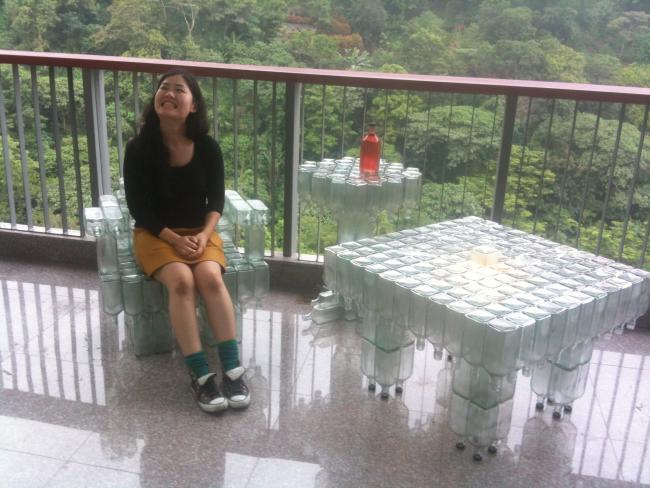
However, traditional ecobrick constructions (like walls, schools and structures) required so many ecobricks that they weren't practical for the everyday ecobricking household. Working from the emerging methodology of mandalic collaboration, Russell realized that it was essential to lower the barriers in building with ecobricks. In this way, homes and communities wouldn’t need to rely on builders to put their ecobricks to use and a significant bottleneck in the spread and adoption of personal plastic responsibility could be overcome.
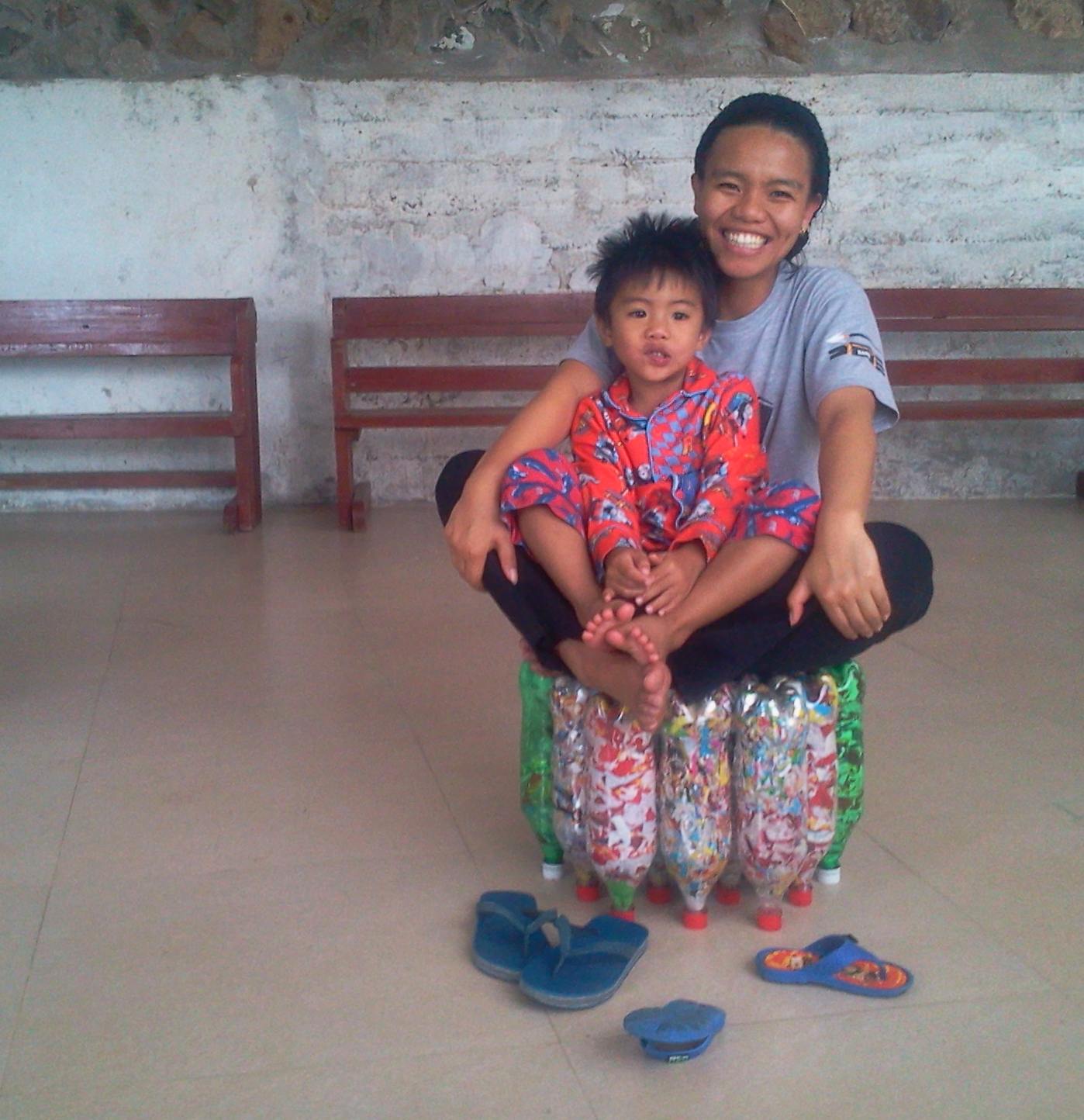
Banague Coteng on the first ever ecobrick Milstein Module on June 14, 2014 in Monkayan, Philippines.
Russell realized that silicone worked just as well to attach plastic bottles together as it did glass. It struck him that with consistently sized ecobricks, the glass bottle building technique could be applied to ecobricks.
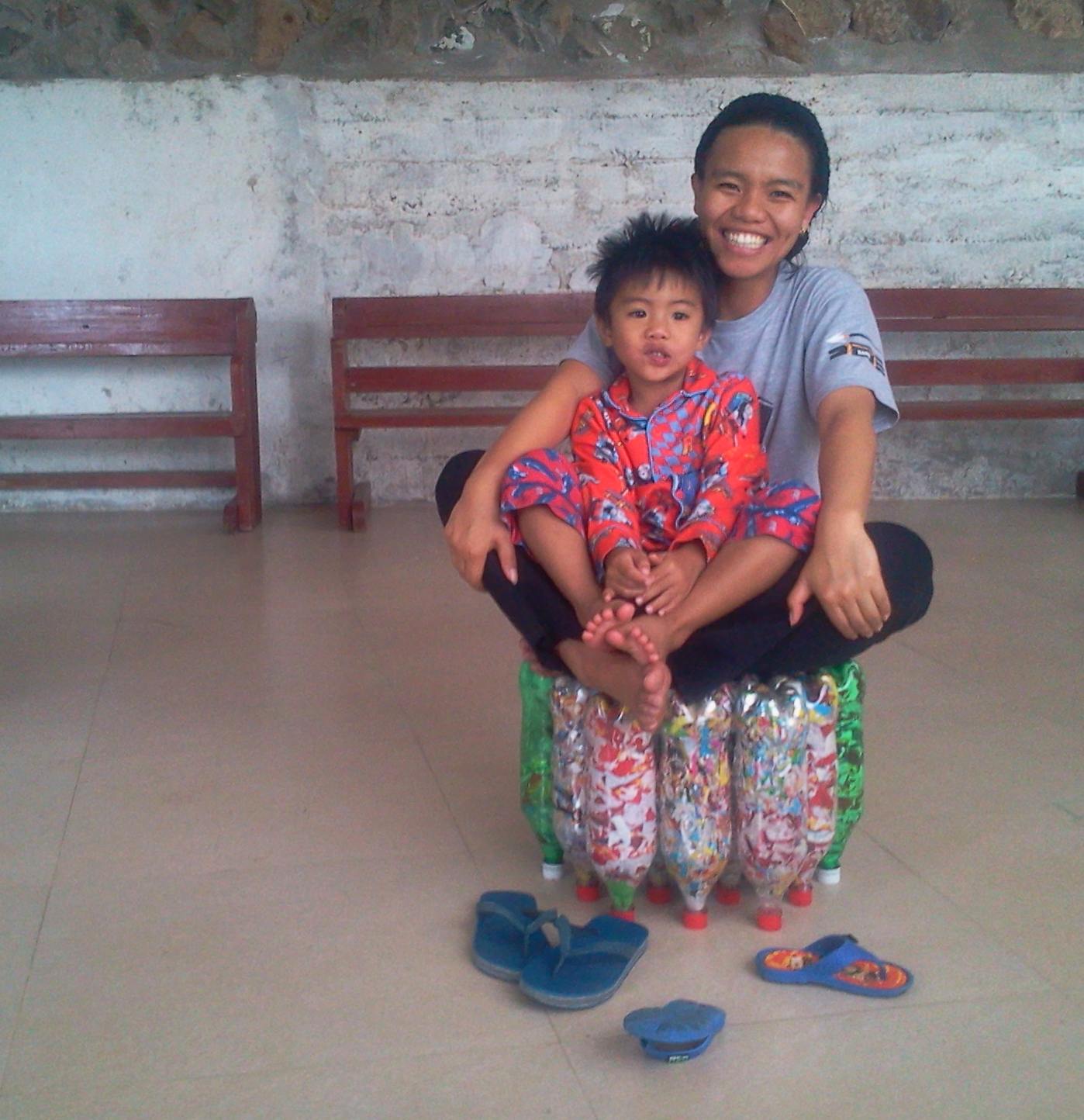
The first ecobrick module was made by Russell Maier and Banague Coteng in Monkayan, 2014. Shortly thereafter, other schools in Tadjian and Balili began to follow suit.
When Russell moved to Indonesia in 2015, Milstein modules were introduced as the primary application of ecobricks. For the first time, in ecobrick workshops, making and building with ecobricks was introduced in the same session. With this simple output-goal, the Indonesian ecobrick movement has spread exponentially. Hundreds of thousands of Milstein modules have been made in Indonesia. The method has since gained popularity in the Philippines and the UK.
Milstein modules are named after a close friend and mentor of Russell, Dan Milstein. Dan, a meditation and Reiki teacher based in California, had spent decades working with inmates in prisons around the world and ex-soldiers. Dan’s mission to bring love and light to those in dark places and discarded by society was an inspiration for Russell while he was stranded in the remote Northern Philippines for five years.

Dan Milstein, Teacher of Peace
Dan supported and encouraged Russell’s parallel work in the early stages of the Asian Ecobrick movement.

Dan encouraged Russell through trying times at the outset of the ecobrick movement. Dan helped accentuate the defining theme of the movement of transforming the perspective of plastic as “waste,” “useless,” or “trash.” Dan encouraged Russell to see the wisdom in the Igorot people he was living with. Dan's own example of “trusting in the universe” in serving people and planet inspired Russell to do the same. Although they never met, Russell and Dan built up a strong friendship. Dan passed away in 2015.
More Modules!
Got thousands of ecobricks? Then maybe you want to consider ecobrick Dieleman Modules! These modules aren't as practical as the Milsteins, but when you've got lots of them, you can build super cool stuff.
An overview of dieleman modules and how they are made.
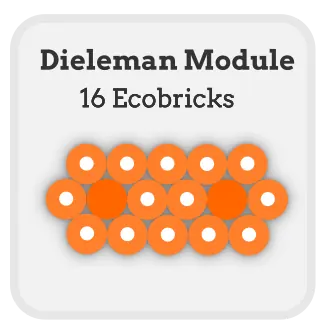
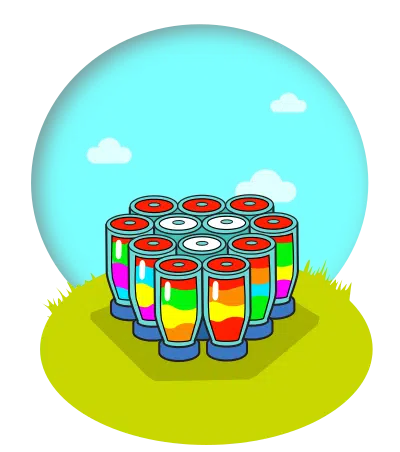
Start with only 12 Ecobricks
To make your first triangle milstein module all you need is twelve ecobricks. Once done, you can keep adding to it to make a hexagon.

Combine Modules
Milstein modules fit together! Combine modules vertically or horizontally to make more furniture.

Then build with Earth!
After your ecobricks have been used in a module or two, then you can spiral them into a long-term earthen construction.
Earth Building
Conception spirale
Les applications Ecobrick suivent les principes de la conception Earthen pour intégrer le plastique dans des cycles de réutilisation plus en plus enrichissants.
En savoir plus
Le principe spirale Terrestre
